This website uses cookies so that we can provide you with the best user experience possible. Cookie information is stored in your browser and performs functions such as recognising you when you return to our website and helping our team to understand which sections of the website you find most interesting and useful.
Process Engineering Support – Fuel Cells
Powerhouse Engsolve was contracted by an established provider of fuel cells to the global market to support them in their process engineering and provided a front-end engineering design (FEED) package for the customer.
The work involved a series of teleconferences and site visits to gather the required information and to understand the client’s requirements for the FEED.
A heat and mass balance was developed for the process, enabling preliminary line sizing and equipment specification to be completed, and utility requirements identified. Process simulation models were developed to predict the pressure profiles for each of the fluids within the system.
In preparation for a HAZOP study, P&IDs were produced along with a line list, equipment list and a Cause & Effect Chart. A high-level pressure relief strategy was also completed. To support the operating cost estimate, a market review of carbon dioxide scrubbing options was undertaken.
The client has a thermoplastic vulcanisate facility in South Wales where a number of world scale extrusion-based production lines are located. As a result of increased worldwide demand for these leading-edge technology products, they have recently significantly expanded their production capability at their South Wales facility in an on-going plan to supply the worldwide market in the most cost-effective manner. The expansion detailed design was carried out by a large UK based design house overseen by a client engineering team.
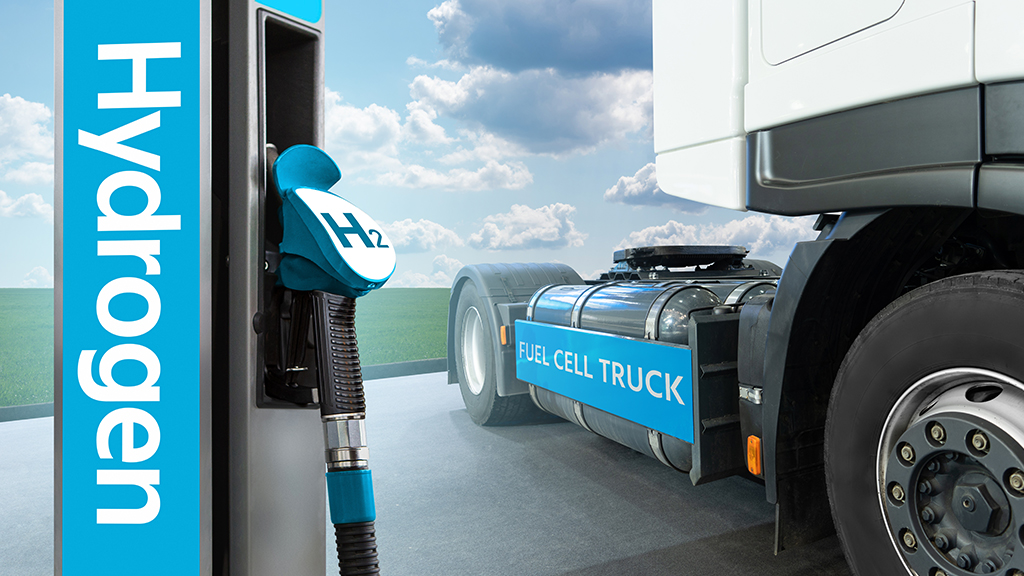